光学薄膜一般可通过化学气相沉积和物理气相沉积两种工艺获得。在物理气相沉积方法中,根据膜料汽化方式的不同,又可分为热蒸发、溅射、离子镀技术,但各种方法都存在自身的优缺点。由于溅射法具有膜厚可控性和重复性好;薄膜与基片的附着力强;膜层纯度高;使用不同材料同时溅射可以制备混合膜、化合膜等特殊材料的薄膜等优点,本论文采用中国科学院沈阳科学仪器研制中心有限公式研制的JGP-560型超高真空多功能磁控溅射系统,以反应溅射法制备满足光学水晶低通滤波器设计要求的可见光增透、近红外截止的光学薄膜。
3.1.1磁控溅射原理
溅射是一个极为复杂的物理过程,涉及的因素很多。溅射是动量转移过程,所以溅射出的粒子具有反向性。粒子和固体表面相互作用的关系及各种溅射产物,都伴随着离子轰击,或由固体表面溅射出中性原子或分子等多个作用过程。实际进行溅射时,一般是让被加速的正离子轰击阴极靶,故也称此过程为阴极溅射。
溅射镀膜是基于载能离子轰击靶材时的溅射效应,而整个溅射过程均是建立在辉光放电的基础上,即溅射离子都来源于气体放电。辉光放电是在真空度约为0.1~10Pa的稀薄气体中,两个电极之间加上电压,而产生一种气体放电的现象。溅射过程就是利用了辉光放电阶段。
磁控溅射中的放电过程是异常阴极辉光放电,放电产生的等离子体为Ar+,尽管也受到磁场同样的洛伦兹力,但由于Ar+靠近阴极,且其质量大,惯性很大,当Ar+跑向靶面时,受磁场的影响很小。因此,大离子基本上是垂直撞击靶面。靶材表面原子由于受高能Ar+轰击而被轰出表面。当溅射的原子到达衬底后,由于粘附力的作用,其中大部分沉积在衬底上形成薄膜。磁控溅射放电基本上克服了二极溅射的低速高温的致命缺点,沉积速率较后者大为提高。同时,它又保持了溅射镀膜的优点,即溅射粒子到达衬底时动能很大,因而粒子在衬底表面的扩散速率相应增大,薄膜生长过程中的阴影效应相应减少。这样,薄膜中的空隙变得更小、更少,薄膜更致密。
光学薄膜一般可通过化学气相沉积和物理气相沉积两种工艺获得。在物理气相沉积方法中,根据膜料汽化方式的不同,又可分为热蒸发、溅射、离子镀技术,但各种方法都存在自身的优缺点。由于溅射法具有膜厚可控性和重复性好;薄膜与基片的附着力强;膜层纯度高;使用不同材料同时溅射可以制备混合膜、化合膜等特殊材料的薄膜等优点,本论文采用中国科学院沈阳科学仪器研制中心有限公式研制的JGP-560型超高真空多功能磁控溅射系统,以反应溅射法制备满足光学水晶低通滤波器设计要求的可见光增透、近红外截止的光学薄膜。
3.1.1磁控溅射原理
溅射是一个极为复杂的物理过程,涉及的因素很多。溅射是动量转移过程,所以溅射出的粒子具有反向性。粒子和固体表面相互作用的关系及各种溅射产物,都伴随着离子轰击,或由固体表面溅射出中性原子或分子等多个作用过程。实际进行溅射时,一般是让被加速的正离子轰击阴极靶,故也称此过程为阴极溅射。
溅射镀膜是基于载能离子轰击靶材时的溅射效应,而整个溅射过程均是建立在辉光放电的基础上,即溅射离子都来源于气体放电。辉光放电是在真空度约为0.1~10Pa的稀薄气体中,两个电极之间加上电压,而产生一种气体放电的现象。溅射过程就是利用了辉光放电阶段。
磁控溅射中的放电过程是异常阴极辉光放电,放电产生的等离子体为Ar+,尽管也受到磁场同样的洛伦兹力,但由于Ar+靠近阴极,且其质量大,惯性很大,当Ar+跑向靶面时,受磁场的影响很小。因此,大离子基本上是垂直撞击靶面。靶材表面原子由于受高能Ar+轰击而被轰出表面。当溅射的原子到达衬底后,由于粘附力的作用,其中大部分沉积在衬底上形成薄膜。磁控溅射放电基本上克服了二极溅射的低速高温的致命缺点,沉积速率较后者大为提高。同时,它又保持了溅射镀膜的优点,即溅射粒子到达衬底时动能很大,因而粒子在衬底表面的扩散速率相应增大,薄膜生长过程中的阴影效应相应减少。这样,薄膜中的空隙变得更小、更少,薄膜更致密。
3.1.2溅射镀膜设备简介
本论文制备薄膜采用中国科学院沈阳科学仪器研制中心有限公式研制的JGP-560型超高真空多功能磁控溅射系统,示意图如图4-1所示。本系统主要包括:真空主溅射室、真空进样室、主溅射室抽真空系统、进样室抽真空系统、真空系统电源控制柜、溅射系统电源控制柜、机械手。可用于溅射生长单层膜、多层膜、介质膜、金属膜、磁性薄膜和半导体薄膜等。
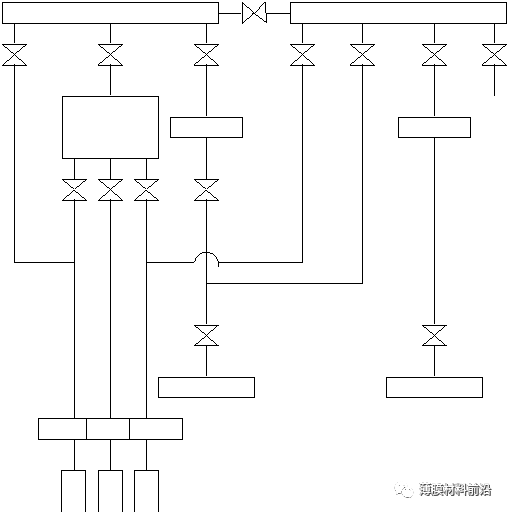
图3-1 JGP560型超高真空多功能磁控溅射系统
真空主溅射室的真空度可以达到6.0×10-6 Pa,用来溅射和沉积薄膜。主溅射室内部下底盘上有五个磁控靶,靶极设有遮挡板,在计算机控制下,打开或遮挡靶位。磁控靶的直径为60mm,采用竖直向上溅射成膜的结构形式。工作时各靶均用循环水冷却,以确保不至于因溅射时离子的轰击而使其温度过高。主溅射室上部有可旋转的圆形样品大转盘,转盘上均匀分布有6个样品放置位,可放样品最大半径为30mm,其中一个样品位上有加热丝,可将基片最高加热到400℃,并采用温度控制器进行控温操作。样品大转盘的转动是由步进电机驱动,通过计算机可以控制基片旋转到设定靶位。样品位上可加直流负偏压,以提高成膜质量。靶相对于基片位置在40~80mm范围内可调。进样室的真空度可达到4×10-6Pa,其内可用来传输衬底、衬底预处理、存放样品、反溅射等操作。
JGP560型超高真空多功能磁控溅射系统配备了两套抽真空系统,主溅射室和进样室可以各自独立使用也可以同时使用,同时使用时,必须关闭主溅射室和进样室之间的阀门G2,将两室分开。两套抽真空系统都为两级真空系统,一级为机械泵、二级为分子泵,两级之间的开关状态是用电磁阀来控制的。当系统内处于大气状态时,开启机械泵,打开预抽通道V5,将进样室和主溅射室的气压抽至低于20Pa后,关闭预抽通道V5 (这样做的目的就是要保证分子泵两端气压低于20Pa的工作条件)。再开启分子泵,开启机械泵与分子泵之间的电磁阀,开启分子泵与溅射室之间的阀门G1。
磁控溅射系统最大优点即为掺杂,一次可放入多个靶材,靶材可以由多种成分制成,从而做到掺杂。还可以通过计算机控制在不同靶材之间切换生长,从而生长出多层膜而无需拿出主溅射室。
3.1.3直流反应溅射制备薄膜流程
溅射法是一种比较成熟的薄膜制备技术,直流反应溅射是在溅射时通入反应气体,使其与靶材发生化学反应,从而得到与靶材完全不同的新物质膜。图4-2给出了直流反应溅射法制备TiO2薄膜的工艺流程。

图4-2 直流反应溅射法工艺流程图
(1)基片清洗
基片表面平整光滑影响薄膜的反射光性能。所以镀膜前必须对基片进行清洗和烘干以去除基片表面污物和化学物质。
(2)抽本底真空
本底真空一般应控制在
以上,以尽量减少真空室腔体内残余气体,保证薄膜的纯洁度。
(3)加热
烘烤的作用是使基片表面出气取水,提高膜-基结合力;消除薄膜应力,提高膜层粒子的聚集度。一般选择在150~200℃之间。
(4)氧氩分压
直流溅射需要满足辉光放电的气压条件,一般选择在0.01~1Pa范围内。当真空度达到要求后,根据试验需要通入氩气和氧气,调解气体的流量和比例。
(5)预溅射
预溅射是通过离子轰击的方法去除靶材表面的氧化膜(由于靶材材料易氧化,在其表面形成的一层氧化薄膜)以及其它非靶材物资。
(6)溅射
溅射时建立在等离子体的条件下,氩气电离后形成正离子高速轰击靶材表面,使钛靶粒子溅射出来并与氧气发生氧化反应生成二氧化钛,达到基片表面形成薄膜。
3.2 TiO2薄膜光学常数的测量和计算
为了研究TiO2薄膜的光学性质,计算其光学常数。我们以光学水晶为衬底,采用金属钛靶进行直流反应溅射镀制TiO2薄膜,制备参数为:本底真空5×10-4Pa,溅射功率为150W,氧气和氩气比为10:20ml/min,衬底温度为室温,工作气压2Pa,靶基距50mm,镀膜时间60分钟。
3.2.1 TiO2薄膜的透射谱
为了研究薄膜的光学透过性,计算其光学常数,我们对光学水晶衬底和制备的TiO2薄膜,利用日本岛津公司的UV-1601紫外可见光谱仪在200~800nm的波长范围内,按1nm的扫描步长进行了透射光谱测量,其透射光谱如图4-3所示。
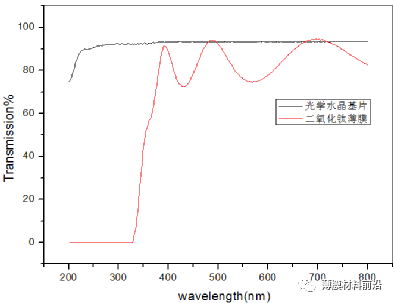
图4-3 光学水晶衬底和TiO2薄膜的透射光谱
从透射光谱图4-3可以看出:(1)镀膜后的透射率发生了变化,TiO2薄膜在300~370nm的紫外波段有较强的吸收,透射率较低特别是在200~320nm透射率为零,而在450~760nm的可见光范围内透射率很高,最高可达95%;(2)透射光谱在可见光区有明显的干涉条纹,且干涉条纹的周期不断发生变化。明显的干涉条纹和较大的调制深度表明薄膜具有很好的光学质量[38]。
3.2.2 TiO2薄膜的折射率计算
为了计算TiO2薄膜的光学常数,利用透射光谱,采用“包络法”可以计算薄膜的折射率、厚度、吸收系数和消光系数。以光学水晶为衬底的TiO2薄膜的包络图谱,如图4-4所示。
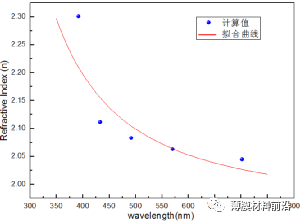
图4-4 TiO2薄膜的透射谱包络图谱 图4-5 TiO2薄膜的折射率与波长的关系
采用“包络法”计算薄膜的折射率是基于下面的两个公式[39-41]:
(4-1)
(4-2)
式中,
和
是对应于波长
的最大和最小透过率(如图4-4所示),
是波长为
时,光学水晶衬底的折射率,计算得到的薄膜的折射率与波长呈现出典型的电子带间跃迁的色散关系,如图4-5所示。其中实点为计算得到的值,实线为拟合的曲线。由图4-5可以看出,当波长从700nm减小到400nm时,折射率从2.03增加到2.20。
3.2.3 TiO2薄膜的厚度计算
薄膜厚度的计算是基于下面的公式[39-41]:
(4-3)
其中,M是两个最大(或最小)透过率之间的峰值(或谷值)的数目,通常取为1,
和
是相邻最大(或最小)的峰值(或谷值)对应的波长,
和
是相应的折射率。结合透射谱,利用(4-3)式,我们可以得到一系列
厚度值,取平均得到
,然后利用双光束干涉公式[39-41] :
(4-4)
式中是对应于最大值的整数或最小值的半整数,利用(4-4)式得到一些列的
,取
最近临的整数或半整数,得到修正的
,然后再利用双光束干涉公式(4-4)及
和
,计算得到一些列
值,取平均得到TiO2薄膜的平均厚度
。具体计算结果如表4-1所示,最终得到的薄膜的平均厚度为348.6nm。
表4-1 TiO2薄膜厚度的计算结果

| 
| 
| 
| 
| 
| 
|
702 | 2.04457 | 360.657 | 2.1008 | 2 | 343.348 | 348.6 |
492 | 2.08281 | 3.0526 | 3 | 354.328 |
392 | 2.30050 | 4.2331 | 4 | 340.795 |
570 | 2.06272 | 2.6103 | 2.5 | 345.417 |
433 | 2.11136 | 3.5172 | 3.5 | 358.893 |
3.2.4 TiO2薄膜的吸收系数的计算
当薄膜的厚度已知时,还可通过透射谱计算薄膜的吸收系数
,计算公式[39-41]为:
(4-5)
图4-6是根据透射谱计算得到的吸收系数与波长的关系,图中薄膜在可见及近红外区域为低吸收区域,这与透射谱中反映的高透过是一致的,在本征吸收边以外,发现了一些对应于杂质吸收的吸收带。这是由于在禁带中,杂质形成了一些分裂的能级,当杂质的含量增加到足够高时,杂质的波函数就会重叠,形成了一个杂质能带,从而在吸收谱上表现了出来。
图4-6 TiO2薄膜的吸收系数与波长的关系
3.2.5 TiO2薄膜的消光系数的计算
薄膜的消光系数
可以利用前面求得折射率和薄膜厚度从透射光谱中计算得到[42]:
(4-5)
图4-7所示为计算得到的消光系数与波长
的关系。可见消光系数随着波长的增加而下降,在近红外区有上升趋势。在可见光区消光系数数量级为
,这一非常小的值表明薄膜具有良好的透明性和均匀性。
3.3单层SiO2减反射膜的初步制备
由于SiO2薄膜与石英玻璃衬底的折射率非常接近,都在1.46附近,所以我们尝试在折射率为1.52左右的K9玻璃衬底上采用磁控溅射法制备了单层SiO2薄膜作为减反射膜,按照单层减反射膜的设计理论,单层SiO2的厚度在94nm左右。主要研究沉积SiO2薄膜时工作气压和衬底温度这两个工艺参数对增加可见光透过率的影响。
3.3.1 SiO2沉积气压对增透效果的影响
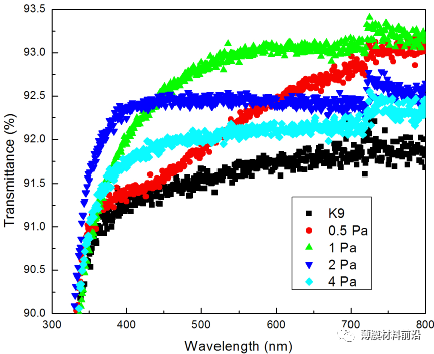
上图是k9玻璃衬底和在不同气压下沉积了SiO2单层减反射膜的k9玻璃在300-800nm范围内测量的透过率曲线。从上图可见,在k9玻璃衬底上沉积单层SiO2能够增大可见光范围的透过率,但是增加的幅度并不大,这主要是因为SiO2的参考折射率1.45虽然小于衬底K9玻璃的折射率1.52,但还远大于单层减反射膜的理想折射率1.23,所以增透效果有限。同时可以看出,在1Pa气压下沉积的SiO2单层减反射膜增透效果较好,在550nm处可见光的透过率可以从未镀膜状态时的91.5%提高到92.8%,如果玻璃正反两面都镀膜的话将可以达到94%左右。
3.3.2 SiO2沉积温度对增透效果的影响(自己写几句话)
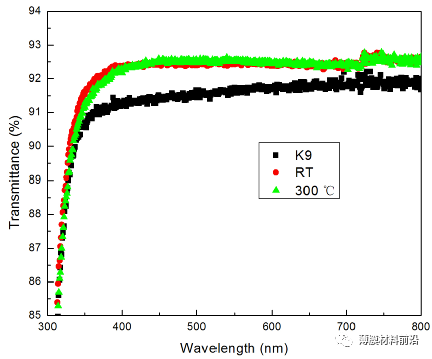
沉积温度对SiO2单层减反射膜增透效果影响较小。